The GT10C is an important development in gas turbine technology, representing a significant improvement in modern power generation capabilities. This advanced machine combines state-of-the-art engineering with practical features for operation, making it essential for both industrial and utility applications.
With its strong design and advanced performance metrics, the GT10C delivers exceptional power output while maintaining high efficiency levels. The turbine’s innovative features address critical industry demands:
- Enhanced Operational Flexibility – Rapid start-up and load-following capabilities
- Improved Efficiency – Advanced aerodynamics and cooling systems
- Environmental Compliance – Low emission technologies
- Reliable Performance – Proven durability in diverse operating conditions
For industry professionals and stakeholders, understanding the GT10C’s capabilities is crucial for making important decisions. This knowledge affects investment strategies, maintenance planning, and long-term operational forecasts. The turbine’s role in shaping future power generation solutions makes it essential for anyone involved in energy infrastructure development.
Understanding the GT10C Gas Turbine
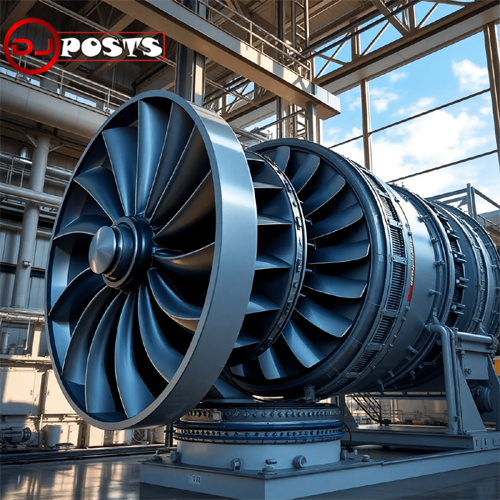
The GT10C is a prime example of cutting-edge gas turbine engineering, with impressive specifications that set new industry standards. This powerful machine delivers an output range of 25-30 MW, operating at a base efficiency of 36% in simple cycle configuration. When integrated into combined cycle systems, the efficiency jumps to an remarkable 53%.
Key Design Features:
- Advanced aerodynamic blade design
- Dual-fuel capability for operational flexibility
- Modular construction for easier maintenance
- Integrated control system with remote monitoring
- Low emissions technology
Alstom, the manufacturer behind the GT10C, brings over 100 years of turbine engineering expertise. The company’s dedication to innovation has resulted in over 7,000 gas turbines installed worldwide. Their research and development center in Baden, Switzerland, serves as the primary hub for continuous technological advancement in turbine design.
The GT10C represents a significant evolution from its predecessor, the GT10B. Notable improvements include:
Performance Enhancements:
- 15% increase in power output
- 2% higher simple cycle efficiency
- Reduced startup time from 15 to 10 minutes
- Extended maintenance intervals
- Enhanced load-following capabilities
Structural Improvements:
- Reinforced rotor design
- Upgraded bearing system
- Advanced coating technology
- Improved sealing system
- Enhanced cooling technology
The turbine’s design incorporates state-of-the-art materials, including nickel-based superalloys in critical components. These materials enable higher operating temperatures and improved durability, resulting in extended service life and reduced maintenance requirements.
The GT10C’s control system features advanced digital technology, allowing for precise operation and real-time monitoring. This system enables operators to optimize performance parameters and respond quickly to changing load demands, making it particularly suitable for grid stabilization applications.
Technical Features of GT10C
The GT10C’s remarkable performance comes from its advanced 11-stage axial flow compressor design. Each stage has carefully designed rotating and stationary blades that work together to compress incoming air. The compressor achieves a pressure ratio of 15.6:1, which is a significant improvement in turbine technology.
Key Features of GT10C’s Compressor Design
- 11-Stage Axial Flow Compressor: The compressor consists of multiple stages, each contributing to the overall compression process.
- Precision Engineering: The rotating and stationary blades are engineered with high accuracy to ensure optimal airflow and efficiency.
- Progressive Compression: As air passes through each stage, it undergoes a gradual increase in pressure, resulting in efficient compression.
Variable Inlet Guide Vanes (VIGVs) for Enhanced Performance
The variable inlet guide vanes (VIGVs) are an important innovation in the GT10C’s design. These adjustable components optimize airflow under different operating conditions:
- Automatic adjustment based on load requirements
- Enhanced part-load efficiency
- Reduced fuel consumption during varying power demands
- Improved startup characteristics
Advanced Cooling Mechanisms for High Temperature Operation
The GT10C uses advanced cooling mechanisms to maintain optimal performance at high temperatures. The cooling system includes:
- Film Cooling Technology: This technique creates a protective air barrier around hot components, extending their lifespan and reducing maintenance needs.
- Internal Cooling Channels: Strategically placed throughout the turbine blades, these channels ensure efficient heat dissipation and maintain material integrity.
Impressive Thermal Efficiency and Operating Capabilities
Through its innovative cooling design, the turbine achieves a thermal efficiency of 36%. It can operate at combustion temperatures exceeding 1,100°C, thanks to high-temperature resistant materials and sophisticated cooling circuits. This advanced cooling architecture allows the GT10C to deliver consistent performance while safeguarding critical components from thermal stress.
Additional Temperature Resistance with Ceramic Coatings
The integration of ceramic thermal barrier coatings provides extra temperature resistance, enabling prolonged operation at elevated temperatures without compromising structural integrity or performance metrics. These coatings are part of a broader strategy that includes insights from NASA research on gas turbine technology, further enhancing the capabilities of the GT10C turbine.
Emission Control Technologies in GT10C
The GT10C sets new standards in environmental performance through its cutting-edge emission control systems. At the heart of these innovations lies the Advanced Environmental Vortex (AEV) burner – a revolutionary technology designed to minimize harmful emissions while maintaining optimal combustion efficiency.
How the AEV Burner Works
The AEV burner employs a sophisticated vortex-based combustion process that:
- Creates a uniform fuel-air mixture distribution
- Maintains stable flame characteristics
- Reduces hot spots that typically lead to NOx formation
- Enables lean premixed combustion
Achieving Remarkable Emission Reduction Results
This advanced burner design achieves remarkable emission reduction results:
- NOx emissions below 15 ppm
- CO emissions under 10 ppm
- Unburned hydrocarbon levels at negligible amounts
Dual Approach: AEV Burner and Selective Catalytic Reduction (SCR)
The GT10C’s emission control system incorporates a Selective Catalytic Reduction (SCR) technology, working in tandem with the AEV burner. This dual-approach system transforms nitrogen oxides into harmless nitrogen and water vapor through a catalytic reaction process.
Continuous Monitoring for Optimal Emission Levels
The turbine’s automated control system continuously monitors and adjusts combustion parameters to maintain optimal emission levels across different operating conditions. Real-time sensors provide instant feedback on:
- Combustion temperature
- Fuel-air ratio
- Exhaust gas composition
- Catalyst performance
These environmental technologies position the GT10C as a leader in clean power generation, meeting and exceeding the most stringent regulatory requirements worldwide. The system’s ability to maintain low emission levels without sacrificing performance demonstrates Alstom’s commitment to sustainable power generation solutions.
How the GT10C Works
The GT10C’s operational excellence comes from its advanced combustion chamber design. At the core of this system is an annular combustion chamber with 18 hybrid burners. These burners create the perfect mixture of fuel and air, ensuring complete combustion while keeping the flame stable under different load conditions.
Key Features of the Combustion Chamber
The combustion chamber has several important features:
- Double-walled construction with advanced thermal barrier coating
- Strategic air distribution ports for enhanced mixing
- Integrated cooling passages for extended component life
- Optimized flame pattern for uniform heat distribution
The Two-Stage Power Turbine
The two-stage power turbine is a significant improvement in energy conversion efficiency. The first stage operates at high temperatures (approximately 1,100°C) and extracts initial energy from hot gases. The second stage, designed with specialized blade shapes, captures more energy at lower temperatures.
How Power Generation Works
Here’s how the power generation process works:
- High-pressure gases from the combustion chamber enter the first turbine stage
- Initial energy extraction drives the compressor
- Remaining energy powers the second stage
- Mechanical energy converts to electrical output via the generator
Flexible Coupling Gearbox System
The GT10C uses a complex flexible coupling gearbox system to manage speed. This system includes:
- Multiple planetary gear sets
- Advanced lubrication systems
- Integrated monitoring sensors
- Adaptive load-sharing mechanisms
The gearbox keeps the right speed ratios between the turbine and generator, adjusting to load changes from 40% to 100%. Operating at 7,700 rpm, the turbine’s output shaft connects to a generator running at either 3,000 rpm (50 Hz) or 3,600 rpm (60 Hz), depending on grid needs.
Speed Reduction Mechanism
The speed reduction mechanism has active vibration control and real-time load monitoring features. It automatically adapts to changing conditions, ensuring smooth operation while protecting important parts from too much stress. With advanced bearing designs and precisely made gear teeth, the GT10C maintains high efficiency throughout its entire operating range.
Condensate Management in GT10C
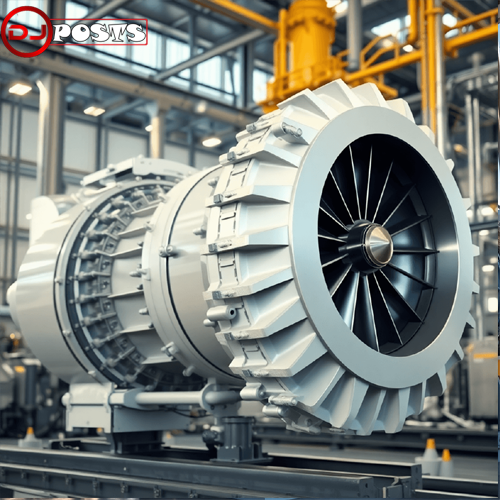
Condensate management is crucial for the efficient operation of the GT10C. The system’s ability to handle water vapor formation during power generation directly affects the turbine’s performance and lifespan.
How GT10C Manages Condensate
The GT10C uses a sophisticated float mechanism to maintain optimal condensate levels. This precision-engineered system includes:
- Primary Float Chamber: Monitors condensate accumulation
- Secondary Safety Float: Provides backup monitoring
- Level Detection Sensors: Ensures accurate measurements
The Three Phases of Trap Unit Functionality
The trap unit functionality operates through a three-phase process:
- Collection Phase: Condensate gathering in designated chambers
- Measurement Phase: Float mechanism assessment of liquid levels
- Release Phase: Controlled discharge through calibrated outlets
Benefits of the Trap System
The GT10C’s trap system maintains consistent pressure differentials, preventing steam loss while efficiently removing condensate. This balanced approach protects internal components from:
- Waterlogging damage
- Thermal stress
- Pressure fluctuations
Preventing Erosion and Maintaining Integrity
The condensate flow path incorporates specialized baffles and channels, directing water away from sensitive components. This design prevents erosion and maintains the integrity of crucial turbine elements.
A network of strategically placed drain points ensures comprehensive condensate removal throughout the system. These collection points feature hardened materials resistant to both high temperatures and corrosive elements, securing long-term reliability.
Applications and Suitability of GT10C
The GT10C gas turbine is highly versatile and can be used in various industries, especially in offshore power generation platforms. Its compact design and strong performance make it an excellent choice for areas with limited space where dependability is crucial.
Key Applications:
1. Offshore Oil & Gas Platforms
- Powers critical drilling operations
- Provides reliable electricity for platform facilities
- Supports emergency backup systems
2. Integrated Development Projects
- Combined heat and power plants
- Industrial complexes
- Municipal power stations
The GT10C’s adaptability shines in remote locations where consistent power supply is essential. Its ability to operate in harsh marine environments while maintaining high efficiency levels has secured its position in numerous offshore installations worldwide.
Recent market success reflects the industry’s confidence in GT10C technology. Alstom has secured significant contracts, including:
- A major supply agreement for North Sea operations
- Multiple units for Middle Eastern offshore developments
- Strategic partnerships with leading energy companies in Asia-Pacific
The turbine’s proven track record in demanding applications continues to drive its adoption across the energy sector. With power outputs ranging from 20 to 30 MW, the GT10C effectively serves medium-scale power generation needs while maintaining optimal fuel efficiency.
Its dual-fuel capability adds another layer of operational flexibility, allowing operators to switch between gas and liquid fuel sources based on availability and economic considerations. This feature proves particularly valuable in remote locations where fuel supply chains may be unpredictable.
Future Predictions for GT10C
The gas turbine industry is on the verge of significant changes, with the GT10C serving as a key player for future innovations. Advanced computational fluid dynamics and digital twin technologies are expected to lead the way in turbine design and performance optimization.
Anticipated Technological Advancements:
- Integration of AI-powered predictive maintenance systems
- Enhanced thermal barrier coatings for higher temperature resistance
- Implementation of hybrid fuel capabilities
- Advanced aerodynamic design modifications for improved efficiency
The development path toward the GT10D and subsequent models will likely include these innovations, pushing operational limits while ensuring reliability. Industry experts predict a 15-20% increase in power output capacity through these technological improvements.
Market Dynamics and Growth Projections:
The high-performance turbine market shows promising growth prospects:
- Rising demand in emerging economies, particularly in Asia-Pacific
- Increased focus on distributed power generation systems
- Stricter emission regulations driving technology adoption
- Growing investment in renewable-compatible power solutions
Research indicates a compound annual growth rate of 4.8% for advanced gas turbines through 2028. The GT10C’s successor models are expected to capture a significant share of this expanding market, particularly in regions prioritizing flexible power generation solutions.
The integration of digital technologies and smart monitoring systems will enhance the GT10C’s competitive advantage. These advancements will enable real-time performance optimization and reduced maintenance downtime, addressing key industry demands for improved operational efficiency.
Challenges Ahead for Successful Deployment
The real-world deployment of GT10C turbines presents several operational hurdles that require careful consideration and strategic planning. Back pressure management stands as a critical challenge, particularly during varying load conditions and different operating scenarios.
Key Operational Challenges:
- Fluctuating exhaust temperatures affecting system stability
- Variable steam flow rates impacting turbine efficiency
- Complex control system integration requirements
- Maintenance scheduling in high-demand environments
The sophisticated nature of GT10C systems demands specialized expertise for optimal performance. Users often face difficulties in maintaining consistent output levels while managing thermal stress on components.
Practical Solutions:
- Implementation of advanced monitoring systems for real-time pressure tracking
- Regular calibration of control parameters
- Strategic placement of pressure relief mechanisms
- Development of comprehensive maintenance protocols
The installation of automated safety systems helps mitigate risks associated with sudden pressure variations. These systems require precise configuration to balance performance optimization with equipment protection.
Risk Mitigation Strategies:
- Detailed site-specific engineering analysis
- Enhanced operator training programs
- Implementation of predictive maintenance schedules
- Regular performance audits and system optimization
Successful deployment also depends on proper integration with existing infrastructure. This includes ensuring compatibility with power distribution networks and auxiliary systems while maintaining operational flexibility across different load profiles.
Conclusion
The GT10C turbine is an example of engineering excellence in power generation. Research and development continue to push boundaries, unlocking new possibilities for enhanced performance and sustainability. As global energy demands evolve, the power industry must adapt through technological advancement and innovation.
The drive toward cleaner technologies shapes the future of turbine development. GT10C’s advanced features and robust design position it as a key player in this transformation. Industry leaders understand that success depends on:
- Continuous optimization of existing systems
- Integration of cutting-edge materials and components
- Development of smarter control mechanisms
- Investment in sustainable solutions
The GT10C represents more than just a power generation unit – it embodies the industry’s commitment to efficiency, reliability, and environmental responsibility. As we look ahead, the ongoing improvement of turbine technology will play a crucial role in meeting global energy needs while advancing toward a more sustainable future.
FAQs (Frequently Asked Questions GT10C)
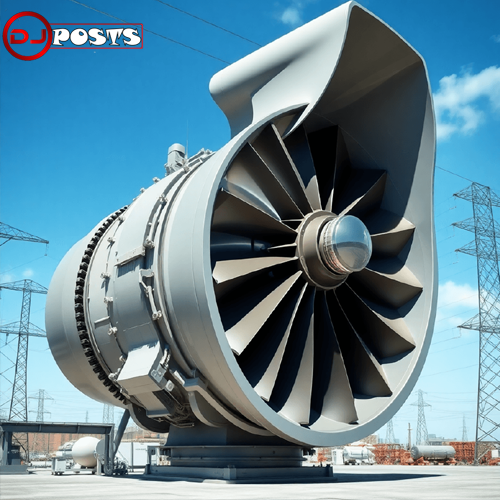
What is the significance of the GT10C gas turbine in modern power generation?
The GT10C gas turbine is significant in modern power generation due to its advanced design features and high efficiency levels. Understanding its capabilities and future predictions is crucial for industry professionals and stakeholders.
What are the key specifications and improvements of the GT10C compared to earlier models?
The GT10C features 11 compressor stages and variable inlet guide vanes that enhance its efficiency. Compared to the earlier model, GT10B, the GT10C incorporates advanced design elements that improve overall performance, making it a more reliable choice for power generation.
How does the GT10C manage emissions effectively?
The GT10C utilizes innovative emission control technologies, such as the Advanced Environmental Vortex burner, which help meet stringent emissions limits for nitrous oxide and carbon dioxide. This ensures compliance with environmental regulations while promoting sustainability.
What role does the combustion chamber play in the performance of the GT10C?
The combustion chamber in the GT10C is crucial for its overall performance as it facilitates efficient thermal energy conversion into mechanical energy. The two-stage power turbine then utilizes this energy for effective power generation.
What applications are best suited for the GT10C turbine GT10C?
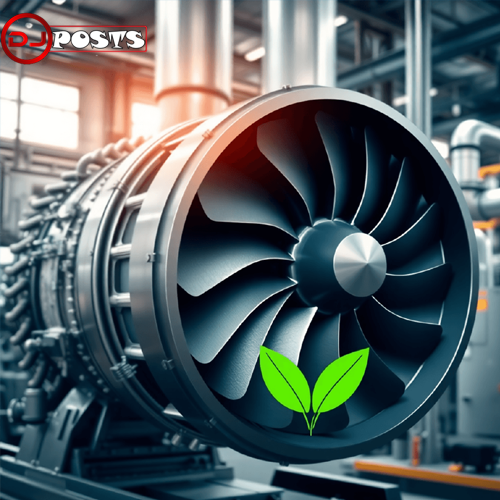
The GT10C excels in various applications, particularly in offshore power generation and integrated development projects that require reliable energy solutions. Alstom has received recent contracts showcasing the turbine’s proven track record in meeting customer demands.
What challenges may arise during the deployment of the GT10C, and how can they be addressed?
Challenges such as managing back pressure effectively during different operating scenarios may arise during deployment. Proposed strategies include implementing operational adjustments and utilizing advanced monitoring systems to overcome these common difficulties faced by end-users.